Ensuring Quality and Safety for McDonald's Suppliers
As a global leader in the food industry, McDonald's maintains rigorous standards for food safety and quality across its supply chain. The McDonald's Supplier Audit Program, developed in collaboration with TUV USA, offers suppliers the opportunity to demonstrate their commitment to meeting McDonald's expectations and ensuring consistently high standards in food safety and quality.
McDonald's places paramount importance on quality and safety throughout its supply chain. The audit program aims to:
- Ensure that suppliers meet McDonald's stringent requirements for food safety and quality.
- Uphold the standards of the McDonald's Supplier Quality Management System (SQMS) and Distributor Quality Management Process (DQMP), which are based on internationally recognized benchmarks such as IFS, BRC, and FSSC 22000.
- Verify compliance with McDonald's-specific requirements to maintain the integrity of the brand and ensure customer safety.
- Enhance transparency and accountability in the supply chain, from production facilities to restaurant operations.
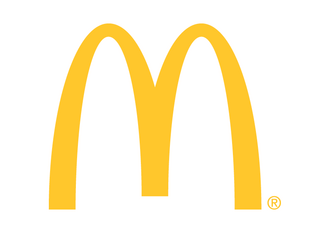
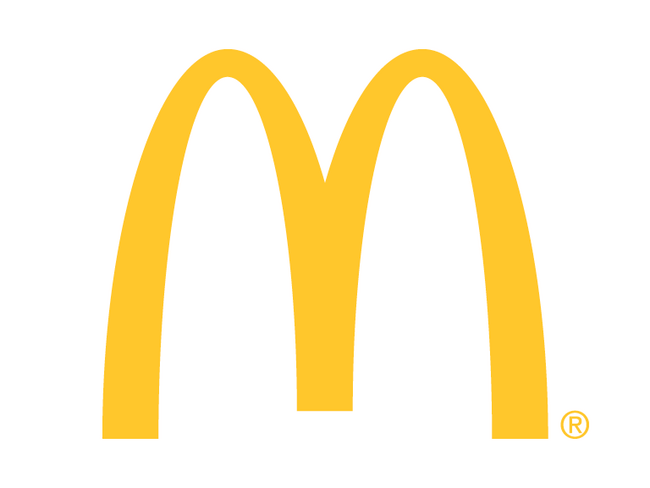
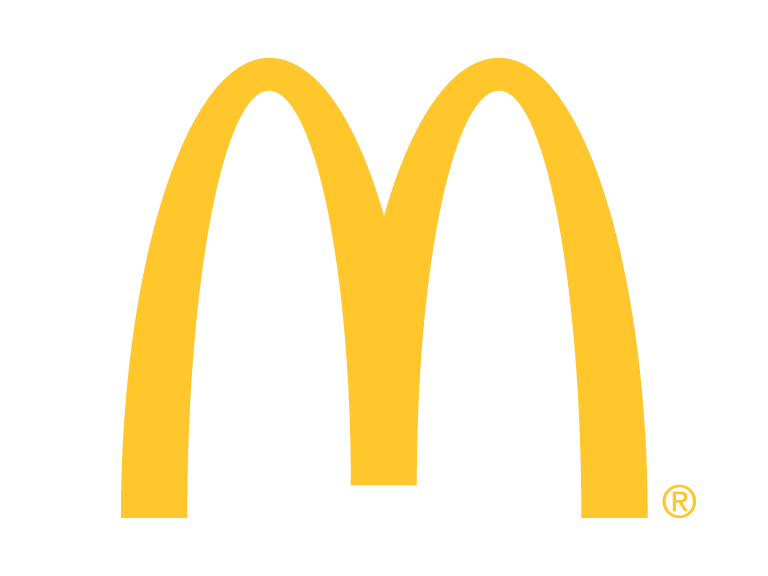
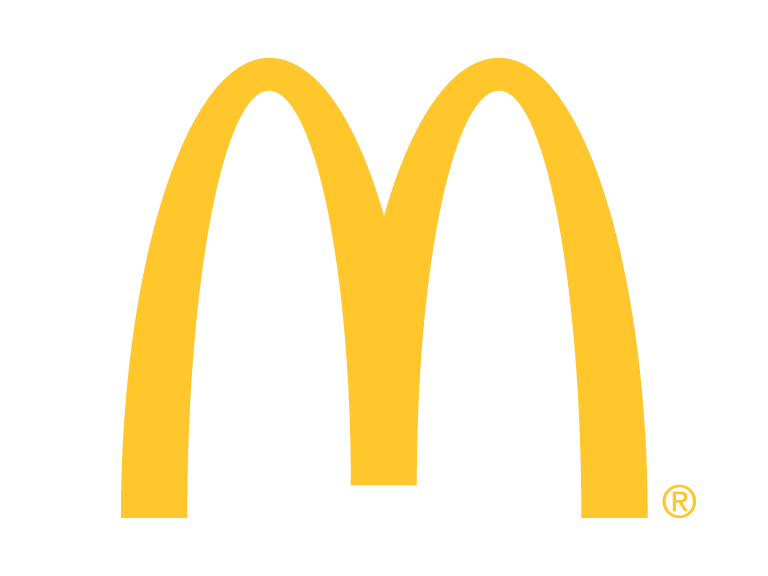
Would you like to contact us?
Benefits of the McDonald's Supplier Audit Program for suppliers:
- Demonstrated Compliance: Audit success demonstrates your ability to meet McDonald's expectations for food safety and quality.
- Enhanced Reputation: Suppliers can enhance their reputation by aligning with McDonald's high standards and commitment to excellence.
- Access to Markets: Compliance with McDonald's standards can facilitate access to new markets and partnerships.
- Continuous Improvement: Participation in the audit program encourages continuous improvement in processes and systems.
- Customer Confidence: Meeting McDonald's standards builds customer confidence and trust in your products and services.
The route to your McDonald's Supplier Audit Report:
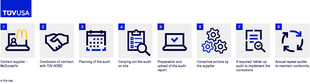
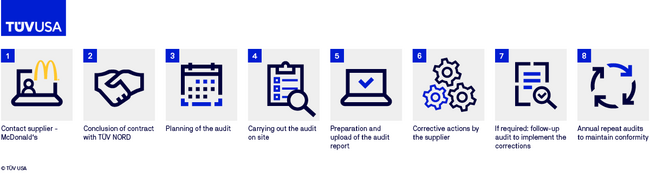
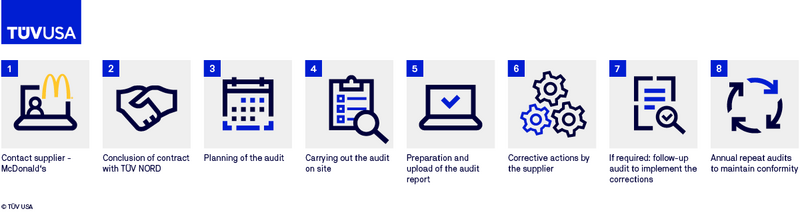
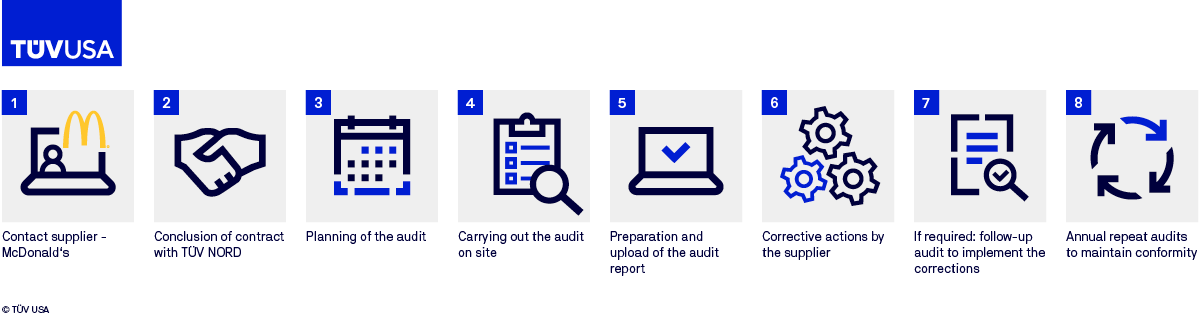
- Your registration with McDonalds: Once your company has successfully registered directly with McDonald’s, we would be happy to offer you the McDonalds Supplier Audit by TUV USA.
- Conclusion of contract with TUV USA: Only after you have registered with McDonalds do you register with TÜV NORD and conclude an audit contract with us.
- Audit planning: The audit is planned taking into account your company’s operational requirements and availability. Please take note that you prepare for the audit independently in advance, considering the instructions and resources that McDonald's provides directly to you.
- On-Site Audit: TUV USA conducts a comprehensive audit, (either the McDonald’s SQMS audit or GFSI standard plus the McDonald’s Addendum), of the supplier's facilities and processes, assessing compliance with McDonald's requirements.
- Audit Report: TUV USA will raise any non-conformities to the supplier and ensure there is clear understanding. Reports for SQMS standalone audits have to be issued within 10 days. The initial Audit reports for GFSI + Addendum audits shall be uploaded within 10 days.
- Corrective Actions: Your company must address any identified non-conformities and implement corrective actions as necessary.
- Possible Follow-Up Audit: McDonald’s may request TUV USA conduct a follow-up audit to verify the implementation of corrective actions.
- Yearly Audit: To remain in compliance with McDonald’s protocol, the audit must be completed annually.
Frequently asked questions on the McDonald's Audit Supplier Program
How do I become a McDonald's supplier?
Each new supplier must be approved and registered with McDonald’s Procurement and Legal Teams before any audits can be delivered. McDonald’s Audit Suppliers cannot perform this initial registration. McDonald’s has very specific requirements and criteria for suppliers, which may vary depending on the type of product being supplied. Once the site has gone through the registration process with McDonald’s, only then can they contact TUV NORD to schedule an audit.
What areas and topcis does the McDonald's supplier audit cover?
The McDonald's supplier audit covers various areas related to food safety, quality, and compliance with McDonald's standards. This may include assessments of manufacturing processes, product quality control, hygiene practices, supply chain management, and adherence to regulatory requirements. Specific topics covered in the audit may vary depending on the type of product being supplied.
What is the objective behind the McDonald's supplier audits?
The primary objective of McDonald's supplier audits is to ensure that suppliers meet the company's standards for food safety and quality. By conducting audits, McDonald's aims to maintain the integrity of its brand, protect the safety and satisfaction of its customers, and promote transparency and accountability throughout its supply chain. Supplier audits also serve to identify areas for improvement and facilitate continuous enhancement of supplier performance.
Your benefits in working with TUV USA
We offer dependable and impartial guidance, backed by our seasoned and proficient team, to assist you throughout the audit process. Leveraging our expansive TUV USA network spanning the globe and tapping into the expertise of diverse specialists, we ensure comprehensive coverage of the international dimensions of your business, thereby ensuring efficiency and transparency in your audit process.
Choosing TUV USA as your certification body grants you access to the globally esteemed TUV brand recognition. Upholding principles of objectivity, neutrality, and expertise, we are dedicated to supporting your success.