Organizations have used system certification as a tool to build up the their management system in order to manage various aspects related to their business like Quality (QMS), Environmental (EMS), Occupational Health & Safety (OHSMS), Food Safety (FSMS), Information Security (ISMS) and others. The benefits of certification were many including a robust management system, customer satisfaction & loyalty, environmental & social compliance, stakeholder’s interest, competition, exports and others.
Today, many of the certified organizations have attained a certain level of maturity with respect to their management systems after having implemented the same for substantial number of years. Over such along period of time, there might be a feeling that the benefits from the management system certifications were declining. Also, quite rightly organizations are now looking for the value addition in maintaining the certification.
Organizations apart from monitoring the improvement overtime and comparing their different parts are also looking to focus on the organization specific issues, including supply chain performance, rather than only on management system standards, which may be considered too generic.
EXPECTATIONS BY THE TOP MANAGEMENTS OF CERTIFIED ORGANIZATIONS –
Management System Performance -
• Apart from Management System Standards, can the audit process also focus on organization – specific issues?
• Is there any methodology to monitor improvement over time?
• Can there be a dashboard to compare different parts of the organisation using similar processes?
• How can the introduction of new standards/requirements be managed along with the existing management systems
Supply Chain Performance -
• continuous improvement monitoring,
• Bench marking between multiple sites or divisions or business units,
• Focus on company’s top priorities, specific issues, client-specific requirements
• Assessing the organization’s suppliers as well as sub-contractors according to a specific referential
CREATING VALUE THROUGH CUSTOMIZED ASSESSMENTS –
The principle of customized assessments is based on the principle that there shall be no compromise on the impartiality principles while delivering the service. The concept of customized assessment depicts an innovative methodology designed to customize the assessment protocol and monitor performance improvement. This allows companies to identify and focus on the primary risk areas in their organization, providing a clear view of their current business performance and its evolution over time. It is however to be noted that customized assessments shall not be performed for organizations certified by the same Certification Body (CB) in relation to those management system standards under the concerned certified accredited scheme.
The approach for customized audits is based on following characteristics:
• Assessment protocols tailor-made to the organisation involved.
• Alignment with Business Objectives through involvement of Top Management.
• Allows an efficient coordination of assessments as well as a tailored interface to the different levels within & outside the organization.
Customized Audits allows possibilities for :
• continuous improvement monitoring,
• bench marking between multiple sites or divisions or business units,
• focus on company’s top priorities, specific issues, client-specific requirements
• assessing the organization’s suppliers as well as sub-contractors according to a specific referential
Modularity of Service :
• Depending on the maturity of system of the organization
• Generic Auditing Approach not limited to certification & can be de-linked or kept independent of system certification process.
Project Model :
Step 1 | Are we in conformance with the requirements? | Requirements can be either the generic international standards (e.g. ISO standards) as well as organization’s specific requirements |
---|---|---|
Step 2 | How to maintain continual improvement? | Identifying in the standards, in excellence models and your own organisation what really matters in terms of performance levels |
Step 3 | How to plan the audits ? | Risk levels to determine priority to check performance levels of most important topics |
Step 4 | How to get the best of what we have? | Using best practices |
Step 5 | How to maintain my performance? | Monitoring along time |
BENEFITS –
Performance improvements & Consistency :
• Better measurement of progress and continuous improvement
• Bench mark of the supplier performance by segment
• Consistent goals, objectives, procedures, terminology and KPIs, allowing benchmarking across sites and over time
• Find and share common solutions. When one issue is solved locally, it can be replicated easily across all Client supply chain
Impact on internal / hidden costs :
• Reduction of non quality – bad service delivery
• Increase of performance of sites / suppliers
• Increase of suppliers selection efficiency
Suppliers’ benefits :
• Integrated approach open to certification opportunity if interested
• Achieve and / or maintain licenses to operate in complying with clients’ and / or legal requirements.
• Differentiate from/align with competitors
• Gain access to new markets/customers
• Offer products conforming to specified level of quality / safety / environmental / social requirements
• Improve partnership and mutual understanding with Client
As always, TUV India is ready to support organizations achieve their goal to have an effective supply chain management complimenting the business requirements by providing training and customized assessment services. TUV India with their expertise in the Quality, Environment, Health & Safety and Sustainability management portfolio and a with large footprint in India can provide assessment services to any location in India.
About The Author
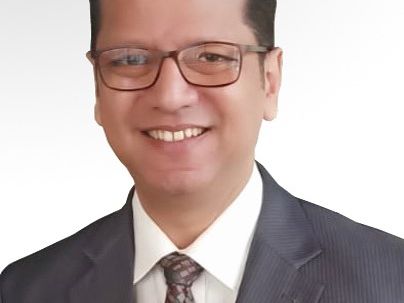
TUV India Pvt Ltd
TUV NORD GROUP
certificationindia@tuv-nord.com