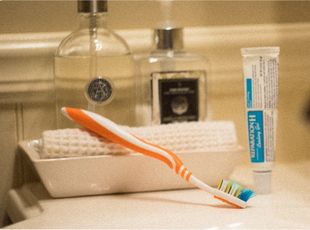
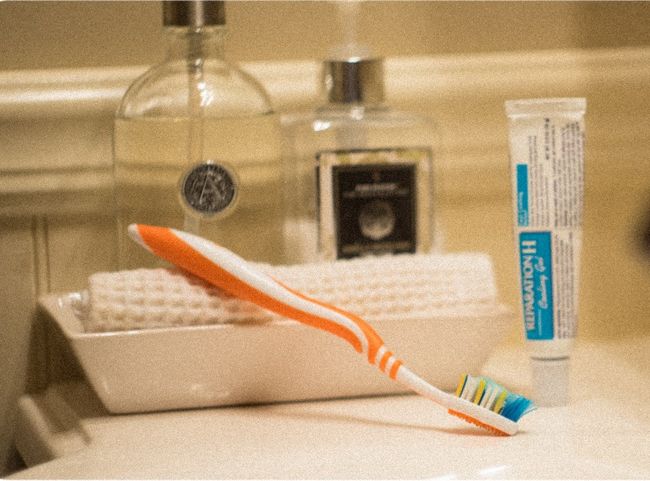
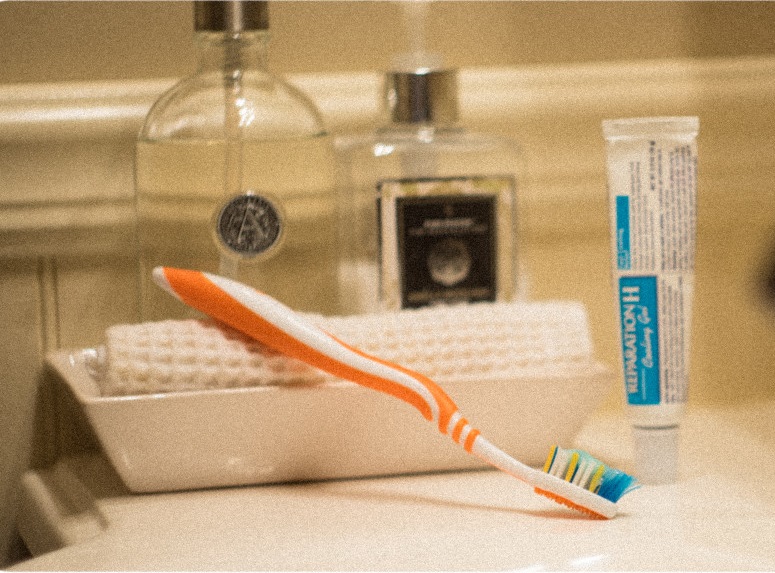
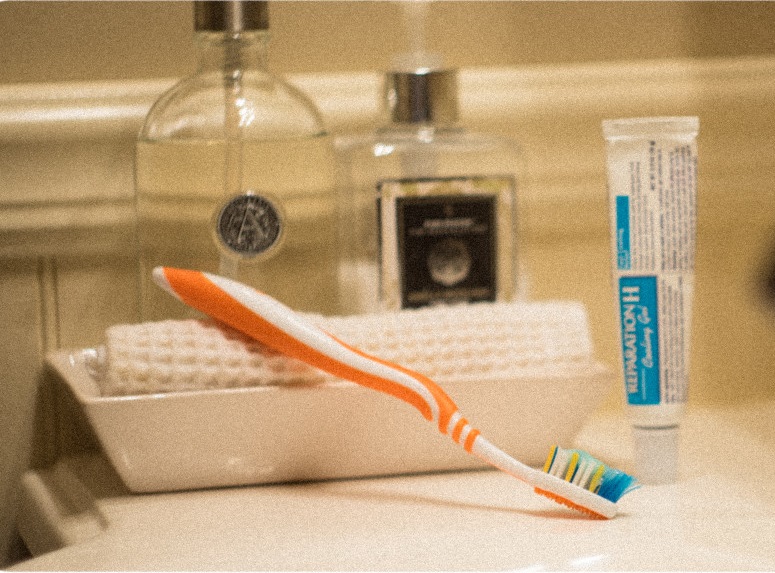
A Quality Management System – any management system, is only as good as the sum of its parts. Lots of things go right, and we all try our best. Yet, out in the world I see the same mistakes over and over again. I want to share those things with you now. Here they are, in a particular order.
1st of 8 Mistakes: Focusing on Manufacturing
A business is a complicated thing. No kidding, it really is. But it is too easy to think that the sections of it that appear to actually produce tangible objects are the most important.
Quite simply – it’s all important. The more you want to get the most out of everything you’ve got, the more important everything you’ve got becomes. If you own a racehorse (and who doesn’t?) it’s easy to think the galloping equine beast is the main… workhorse. But what about the shoes, and the guy who puts them on? (it’s a farrier, but that sounds highfalutin, so I didn’t say it).
And there’s the jockey- and the jockey’s Jockeys, the nutritionist, stable boy – and a whole slew of influential entities. If any of those are non-optimal, do you think the whole system can be optimal?
Many companies I go to have continual improvement projects related to assembly areas but neglect sales departments, or purchasing groups or human resource departments. There are always better ways of doing things, mostly because “better” is an evolving concept. Options need to be considered and tried out in all areas – not just manufacturing.
I’ll take a second to cover the frequent exception. Design functions, along with production, are often targeted for streamlining. Or rather, they become streamlined over time. It may be a stereotype, but engineers tend to find optimum paths somewhat organically. Or they are at least interesting paths.
This may be influenced by two factors. One is that 9001 and the related standards that share design and development pieces with it, provide a good skeleton that hasn’t really changed in lots of years. It just might be a common-sense starting point or the successful modifications to it have traveled from company to company along with the migrations of engineers.
The other factor is, I believe, the cerebral nature of the activity itself. When you get a bunch of brains focused on development, the tendency for self-development; the development of the organism that’s developing – is a genetic inclination. It’s a bit like cleaning your office instead of working – but in a good way.
There’s more to businesses than design or manufacturing; opportunities for improvement abound. One of my favorite quotes encapsulates and summarizes this idea well, “How you do anything, is how you do everything.”
2: Fixing Problems Without Understanding Cause
Up here in the Great White North, we like to think we have “Yankee Ingenuity”. We’re really good at fixing things using creative approaches. Duct tape and elbow grease.
But sometimes we spend lots of effort on the solution, and not enough resource figuring out why the problem happened in the first place. Fortunately, when the problem happens again – we can fix it right quick. Third time’s the charm! Sound familiar?
Some of this is because each of us carries a sort of personal toolbox. We tend to do the things we’re good at. One apt phrase is, “When you know how to use a hammer, everything looks like a nail.”
Fortunately, not only are there different types of hammers, there are other tools that can be brought to good use (what did you call me?!). These help an organization get to the root of the problem, or to a main cause. Since each of them could span a blog entry of their own I won’t do much more than list them here.
• 5 Whys Analysis – Asking “why” multiple times until the culprit is found. Make it so the culprit can’t come back
• Change Analysis – Won’t always generate root cause, but will arrive at a cause. Six step process worthy of further investigation.
• Barrier Analysis – Identifies barriers used to protect a target from harm. The terms are flexible; think shoe/foot/glass. Glass is the threat, shoe is the barrier, foot is the thing to protect. Foot is cut – how, specifically, did the shoe fail?
• Ishikawa (fishbone) diagrams – or any kind of tree diagram. In general, each branch of the tree, or each branching bone of the fish, adds to the understanding of the factors involved. By understanding the factors, countermeasures can be considered.
And on and on – There are so many tools available it just doesn’t make
3: Too Many Corrective Actions
While it may seem counter-intuitive to a continual improvement mindset – it really isn’t. A mature management system is very good at collecting data, then by analyzing that data, it can target areas for improvement.
Writing a NCMR (Non-Conforming Material Report) as if it was a CAR (Corrective Action Request) is a terrible resource-waster. Do this instead when you find nonconforming material:
• Capture the data and look for common failure modes
•Create a set list of failure modes (you may need to adjust this over time)
•Make a Pareto chart of the failure modes
•Create a CAR for the big hitter.
•Do it again for the next biggest hitter.
If you find the same issues continue to arise then see Mistake number 2, above.
Corrective actions are indeed that avenue to improvement but they need to rise above the level of the noise. The noise is the inherent variability in the system; few things are perfect.
Find the trends, then with a healthy use of the corrective action tools like those listed above – focus the limited resources toward determining root cause.
4: Not Auditing Internal Audits
Internal audits should be deep, and thorough and, dare I say – brutal. With internal audits, you won’t make any friends by making friends. Tough love.
The whole system should be checked against existing procedures (documented, or not) and against the requirements of your standard of choice.
The audits should be planned, that plan should be based on some analysis of the status and importance of the areas to be audited.
They should be carried out by qualified individuals who are independent of the function being audited. When problems arise, those corrective actions must be taken without undue delay and the cause of the findings corrected and verified as effective.
Sounds lovely, doesn’t it? Not only do you need to do those things in order to have an effective internal audit program – but the standard requires that you do those things.
A frequent “gotcha” here is if you have a contractor perform your audits. One of the rules is that the auditor must be independent of the thing being audited. Sometimes the contracting company can provide another auditor specifically to audit that function – that could work. Or, you could, given the proper training and procedure, audit the internal audit process as part of Management Review.
Or you could have someone internal to the company and from a department typically outside of the QMS – like accounting, do the audit of audits.
If the audit process itself isn’t checked to make sure it continues to do all of the above, then all of your credibility goes straight out the window. And in through the front door comes a written nonconformance from your friendly ISO auditor.
5: No Dashboard, No Goals
A Dashboard is simply a frequently updated collection of the upper level metrics presented in a way that is quickly and easily digested. Goals for these metrics should be evident. Where the trend of the data is moving significantly away from the goal then there should be an action plan to adjust the trend.
Action plans have owners, they have something that needs doing – and they have accountability.
Sometimes the dashboard includes a collection of charts along a frequently traveled hallway. Who needs to see these things? Anyone that can influence the data – that often means everyone in the organization.
If you do have one of these metrics boards/dashboards do make sure the date is current please.
Nothing says “We really don’t care what’s going on, nor do we care if no one else knows what’s going on” like charts that are four months out of date.
Am I preaching to the choir? Sing with me, my friend.
6: Rework Without Collecting Data
This is fairly common, meaning I see it once or twice a month (I do somewhere around a hundred audits a year; three to five audit days per week).
Example? Take a manufacturing floor, someone builds something – let’s use a contract manufacturer. The assembler does his job and sends it off to an in-process or final inspection step.
The inspector does a nice inspection, using documented and established inspection criteria. They find a missing screw – and record it on their inspection sheet or enter it into a database. They have a box of the correct screws and they correct the problem. Fine – no issues there (ideally yes, someone else checks the fix).
Then they find another screw that’s a bit loose – not that loose, really. They tighten it down. They begin to look at the cosmetic criteria – looks good.
Oops. That loose screw should have been recorded, right? Maybe that missing screw started out as loose (I blame the parents).
This happens more often when everyone is really friendly and there are penalties for failure. So, when Maria in inspection finds something Mary in assembly missed – Maria fixes it and nobody gets hurt. Except the reliability of the product and cost of assembly.
Either make sure nobody likes each other, or don’t attach a stigma to making mistakes (or mistake proof the process!). I’ll leave it up to you to choose.
7: Big Meetings Without Action Items
I’ll keep this one real short.
Don’t have a meeting without action items.
A meeting without action items is called e-mail.
I said “Big” meetings; if two or three people need to exchange data verbally, fine. You define “big”.
Let me assert that Management Review meetings are big meetings. Please have action items.
If you have a meeting, and it turns into a status meeting – and everything looks good, then take the opportunity to change the definition of “good” to “great”.
Change the specification, or bring in the date – at least look at the feasibility of doing it better. If you feel like you’re already at “great” then re-allocate a resource, record some “lessons learned”.
Continual Improvement, my friend, generates Actions.
8th of 8 Mistakes: Taking Classes But Not Learning
Most courses and seminars are PowerPoint snooze-fests in over-air-conditioned rooms where you’re lucky to have a quiz at the end of four days. Just because the data is presented to you – doesn’t mean it has been taught to you, or that you have learned it.
But yes, the lemon Danish was awesome and hey, you got a Certificate.
Certificates are nice, but skills and knowledge brought back to the work environment are like bars of gold-pressed latinum. Time and money are being spent- why not learn something?
Even if you’re a conscientious student executing the study habits that got you through high school or college – you could be retaining a whole lot more.
To most people, underlining and highlighting, rereading, cramming, and single-minded repetition are the extent of their learning repertoire. Recent studies have shown clearly that these skills create the illusion of mastery, and that any gains fade quickly.
Durable learning comes from things like:
• self-testing,
• introducing difficulties in practice,
• waiting to re-study new material until a little forgetting has set in,
• interleaving the practice of one skill or topic with another.
That’s basically the introductory paragraph of the book, Make It Stick: The Science of Successful Learning. I’ve read that book – it is an enlightening and inspiring read.
While there is a wealth of vital material on the internet, and within the corporate training rooms (and those freezing hotel conference rooms), most of it is simply that – material.
Learning is really your responsibility, you can’t rely on an instructor to do it for you. Read. That. Book.
Thank you for listening, I hope you got something useful from the 8 common QMS Mistakes I see regularly. I’d love to hear back from you with something from your own list of painful things.
Author
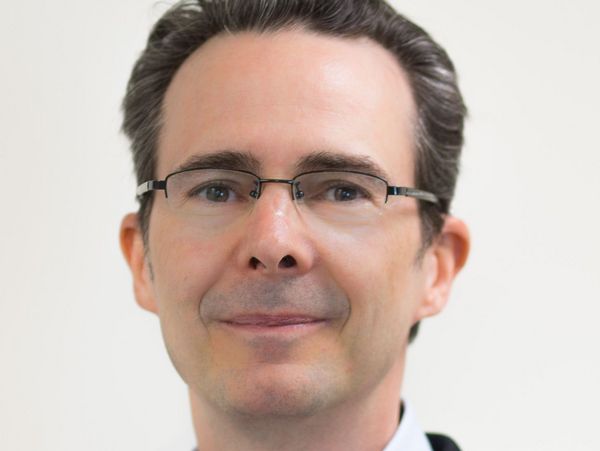